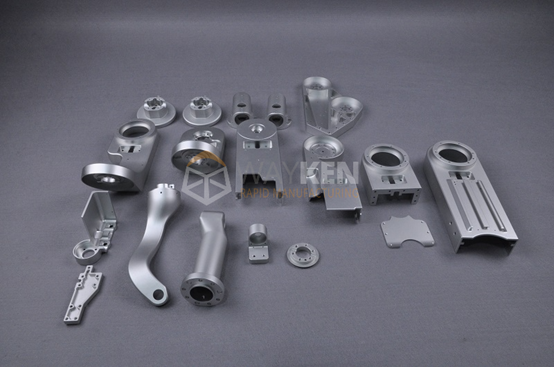
Medical machines like MRI, CT, and PET imaging systems are produced with parts that have high accuracy, are harmless to the body, and protect biological tissue from EMF. To reach these traits, high standards of machining should be applied, most of all for aluminum parts that operate in decisive settings.
Because many issues with tolerance stacking, the finish of surfaces, and radio frequency compatibility are growing, CNC machining gives the best control over the process. Most of these chassis are made from CNC-machined aluminum that is light, corrosion-resistant, and can carry electricity. For medical device prototyping to meet ISO 13485 and FDA requirements, iterative machining and validation loops are needed.
This article looks into the specific CNC strategies that support high-tech diagnostic hardware by ensuring aluminum meets electromagnetic, regulatory, and cleanroom requirements.
Machining Strategies for EM Shielding and Structural Rigidity
CNC machining is based on avoiding EMI by making sure the enclosure is continuous, parting lines are small, and there are almost no micro-gaps. Applying 5-axis milling and following the outline of the parts, engineers cut individual aluminum billets to produce enclosures. With this process, the need for assembly bonding is less, avoiding the problem of impedance mismatches. If a slot’s tolerance is below ±0.02 mm and if its surface finish is improved, it can minimize radio-frequency leakage frequencies from 10 MHz to 1 GHz in MRI machines.
Also, face-milling with specialist hardware and tooling ensures the absence of burrs and the maintaining of signal intensity across the areas that fit together. The process keeps the CNC machined aluminum from losing its shielding power, so no extra coating is required.
Integrating rib patterns and insert interfaces directly into the part based on FEA analysis takes care of the part’s structural problems. During medical device prototyping, simulation planning ensures that the radii and thicknesses are even to help relieve stress and lessen vibration. Some parts of CT scanners are exposed to short, transient mechanical forces from the gantry and rotating modules. Milling with great precision allows the magnet locations and sensor bores to be the same, usually within a 0.015 mm gap.
T6-tempered 6061 or 7075 metal, chosen for its properties and how easily it can be machined. These geometrically complex CNC machined aluminum allow the components to do work by both mechanical and electromagnetic functions at the same time, which checks prototypes and preserves final product reliability.
Regulatory Implications in Medical Device Prototyping Phases
For a manufacturing process to be compliant, it should start with the machining parameters being set and traced digitally. Each round of testing medical devices captures the values of spindle speed, feed rate, signs of tool wear, and in-process measurements. We obtain our aluminum stock tracked by barcodes with the necessary paperwork for confirming suitability and testing. CNC report tracking and review of batch inspection reports permit proper review and submission to the FDA for approval, along with ISO 13485.
For things that are in contact with fluids, choosing the right materials and preparing them well helps guarantee compliance with ISO 10993 on cytotoxicity and sensitization. Commonly, aluminum machined with a CNC process gets Type II or Type III anodizing, strengthening the metal against corrosion and significantly reducing its response to biological influences, while preserving its performance in electrical systems.
Medical device prototyping relies on setting up tooling quickly and adjusting the G-code according to parameters. At the alpha stage, engineers get input from radiologists to perfect the user-friendly nature of the components. Since CNC machining is very accurate, the dimensions of prototypes are the same as those of the finished devices. Because of the fidelity, verification and validation (V&V) are completed faster, and fewer DOEs are required.
Members of a cross-functional team work together to include all the usual RF shielding, the strong supporting load structure, and proper cable handling within a single step in manufacturing. For this reason, CNC machined aluminum is crucial for reaching important regulatory objectives, covering risk analysis to premarket approval.
Cleanroom-Compatible Machining and Anodizing Protocols
All diagnostic parts for cleanrooms should meet at least the standard set by ISO Class 7. Strategies in CNC machining include dust-clearing coolants, mist-capturing systems, and cutting areas that are enclosed. To stop particles from building up on useful surfaces, filters are used on CNC machined aluminum to capture anything smaller than 5 microns.
Once machining is completed, the parts go through several steps for cleaning, including being put in ultrasonic baths, passing through a deionized water rinse, and getting an isopropyl alcohol spray. They clean away carbon substances and small waste particles. After the surfaces are cleaned, temporary ESD-safe films are applied until they join the cleanroom. This contamination control strategy ensures that medical device prototyping parts transition seamlessly from the mill to sterile assembly zones.
The protocol that’s followed depends on how the part is used. Type II anodizing helps preserve the look of non-contact surfaces, whereas Type III hardcoats boost the sliding abrasion resistance of metal. Anodizing causes surfaces to widen; therefore, programmers adjust in CAD and change toolpath calibration to fit the needed dimensions.
There are times when CNC machined aluminum surfaces are left unsealed in order to make secondary adhesive bonding or conductive gasketing easier. In critical areas, electropolishing smooths the surface, which decreases the chances of biofilm building up. After finishing the process, particle counting is done to verify that the product meets Class II or III standards from the FDA. These methods guarantee that aluminum components made with CNC are qualified for strict diagnostic settings in real life.
Conclusion
The use of CNC machining affects how effective, strict to regulations, and simple to use medical imaging systems are. Thanks to following different materials, using cleanroom facilities, and conducting validation, engineers ensure the standard of the parts they make. CNC machined aluminum makes sure that first prototypes and production parts all perform the same, are protective, and can be sterilized. As a result, it remains central to precision-driven medical device prototyping workflows.