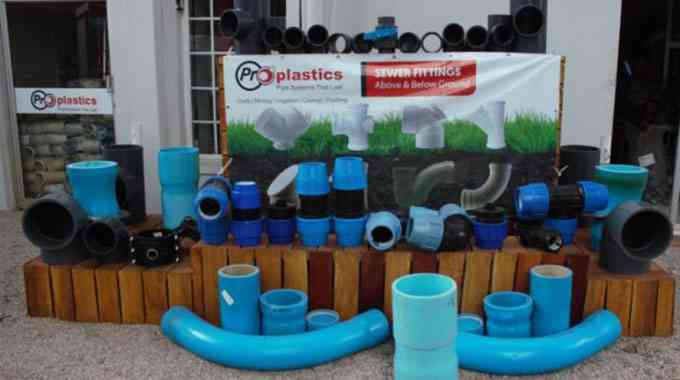
PLASTIC pipe manufacturer, Proplastics Limited (Proplastics) has invested US$3 million in automation technology to boost operational efficiency and streamline its production processes, NewsDay Business has learnt.
In an interview, Proplastics chief executive officer Kudakwashe Chigiya said this investment reduced the number of workers who needed to be physically available for production, cutting operational costs.
Proplastics primarily produces a range of plastic pipes and fittings made from materials like polyvinyl chloride, high-density polyethylene, and low-density polyethylene, used for irrigation, mining, civil construction, borehole casings and cable ducting.
Essentially, the firm specialises in complete plastic piping systems for various industries in Zimbabwe.
“So, we underwent an automation revolution where most of our systems are working on their own without human intervention,” Chigiya said.
“So, it had a positive impact on the employment levels and a negative impact. You know, we are pursuing, rigorously, the industry 5.0 initiative, which is automation.”
However, he explained that the company managed to retain its staff despite the automation process.
“So, once you automate, then it takes out your jobs. We had to reassign all the workers that were affected to other areas. We still have other duties, such as distribution that need people to be physically there. So, we did not necessarily need to retrench,” Chigiya said.
- Power cuts hamper Proplastics production
- Proplastics dumps Zimdollar loans
- Proplastics charms regional market
- Proplastics profit trebles to US$520 000
Keep Reading
“We have invested over US$3 million in automation. In our mixing plant, which you see today, we are hiring about 68 employees. Now we have only four employees that are running that. That is serious automation.”
He noted that the company had 300 workers working at the manufacturing plant.
“So, the total number of employees at the moment, indirectly and directly, in our system is about 300 employees. You will also be able to see that we also operate 24/7 mostly. We shut down during Christmas, and then when we open, on January 15,” Chigiya said.
“And you know, plastic, when you melt it, you really need to make sure that you continue running. We normally have three shifts throughout the day and night.
“For now, in January, because we do not have that high demand so far soon after the first quarter, we will be forced to run almost 24 hours, seven days a week.”
He said the firm invested in the manufacturing plant over a period of three years and poured in US$12 million into it.
“Over the past three years, we have managed to construct a new factory because all the 1965 (the year the company was formed) factories became irrelevant to operations,” Chigiya said.
“We spent some US$7 million, and we put in additional money for production and mixing equipment to ensure the integration of the value chain.”